Overview of Flat Plate Filter Washing and Drying Machine Equipment
The common production process of crystalline drying active pharmaceutical ingredients is: crystallization → filtration → washing → filtration → drying → discharging → powder crushing → sieving → powder mixing → packaging. The traditional and backward process flow is manifested as follows: crystallization tank crystallization → solid-liquid separation by centrifuge (or filter solid-liquid separation) → washing tank cleaning → vacuum filtration → drying by double cone rotary vacuum dryer (or vacuum drying oven) → manual discharge → crushing by crusher → mechanical vibration screening screen → mixing by mixer → manual drum loading.
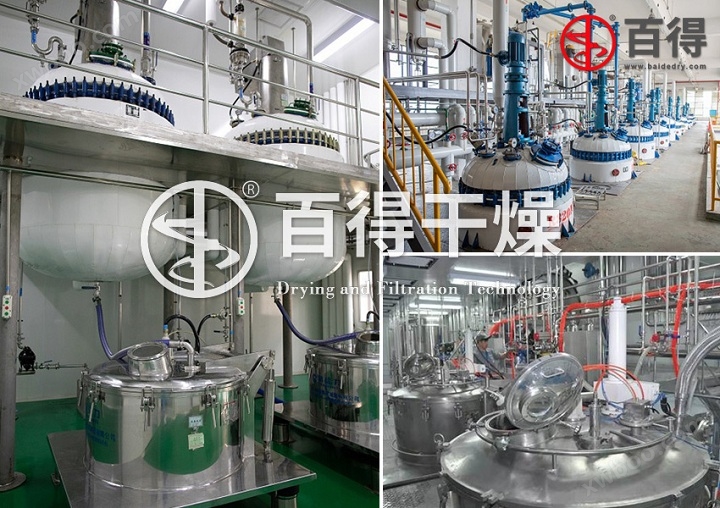
In this process and equipment operation, there were multiple transfers of materials containing crystals, and the use of traditional equipment was limited to some extent. The problems exposed by traditional crystallization drying raw material production equipment and technology are:
1. In the production of materials containing crystals, there will be multiple processes such as turning over the shovel, digging out the powder with the shovel, and rolling the filter cake. This will result in prolonged exposure of the crystals and the formation of cracks in the filter cake, affecting the uniformity of crystal formation and ultimately impacting the quality of the product.
2. Due to the limitations of traditional equipment, materials in production need to be transferred multiple times, which can easily cause cross contamination and make it difficult to meet GMP requirements.
3. The multiple processes, equipment, and simple equipment structure make the operation cumbersome and the production labor intensity extremely high. At the same time, the backwardness of traditional single unit equipment makes it extremely difficult to clean and sterilize batch changes, making it impossible to ensure their effectiveness.
In short, the problems exposed by traditional crystallization drying raw material production equipment and technology are difficult to meet GMP requirements.
Changzhou Baide Drying integrates the traditional crystallization drying process of active pharmaceutical ingredients, making breakthroughs on the basis of inheriting the essence of tradition. Starting from equipment reform, integrate its process and form a new overall process equipment scheme for crystallization drying of active pharmaceutical ingredients; Starting from simplifying the process, the filtration, washing, and drying processes are integrated into one machine, reducing the number of process transitions; Starting from automation, washability, and sterilization, we will improve the overall process to make it more suitable for the production of sterile raw materials.
The overall process equipment scheme for the improved crystallization and drying of raw materials is as follows: crystallization tank crystallization → filtration, multiple washing filtration, drying and discharging of the "three in one" dryer → specially developed pulverization of the crusher → screening of the new vibrating screen → mixing of the mixer → automatic packaging and weighing machine cylinder loading. Among them, most of the processes can be transferred and transitioned using a closed material conveying system.

Structure and Principle of Flat Plate Filter Washing and Drying Machine
The filtration washing and drying machine (commonly known as the "three in one" in the industry) can achieve continuous processes such as material filtration, washing, drying, sterilization, and unloading. Its operation method belongs to batch operation (intermittent operation) and is widely used in the fields of pharmaceuticals, food, pesticides, chemical engineering, etc. The filtration washing and drying machine is mainly composed of a vertical tank body with a pressure bearing part, a heating system, a stirring system (stirring shaft, stirring blade, mechanical seal, etc.), a stirring lifting mechanism, a transmission mechanism, a filtering medium, a discharge valve, a spraying device, a sterilization device, a hydraulic pump station, a main electrical control cabinet (including frequency converter, PLC) and other components, realizing the integration of machine, electricity and instrument.
After the basic operation processes of filtering, washing, drying, and solid unloading of a batch of materials are completed, the filtering, washing, and drying machine can also use solvents to dissolve the materials that need further processing, and continue with the next operation process.

Process flow of flat filter washing and drying machine
1. Filtering
Pour the solid-liquid mixture slurry generated by the upstream reaction kettle or crystallization equipment into the tank of the three in one equipment, and use pressure difference as a driving force to achieve filtration and separation of the solid-liquid mixture. In practical applications, there are methods such as pressure filtration, vacuum filtration, and a combination of pressure and vacuum filtration. Pressure filtration uses clean compressed air, nitrogen or other inert gases, and the specific compressed gas should be selected according to the characteristics of the solid-liquid mixture. For example, if solid-liquid mixtures are prone to oxidation or contain explosive media, compressed air should not be used and inert gases should be used instead. Based on practical experience, the pharmaceutical industry generally requires a filtration pressure of 0.2-0.3MPa to achieve filtration, while some products in the chemical or food industries require higher filtration pressures, with some reaching up to 1.0MPa.
2. Washing
After the filtration process is completed, the next step of the process operation is washing. The three in one equipment tank is equipped with a specially designed spray device, which can evenly distribute the cleaning (washing) solution inside the tank. By opening the stirring system, stirring lifting mechanism, and transmission mechanism, the blade can rotate and move up and down axially, allowing the material to be thoroughly washed and removing impurities adhering to the surface of the grains. The detergent and washing frequency used for washing should be determined according to the characteristics of the material and production process.
3. Dry
The drying process of the three in one equipment can use hot air drying or vacuum drying. When using hot air drying or vacuum drying, clean inert gas must be used because dust will be generated during the drying process, and the operating environment of the equipment should be considered to be explosion-proof. At present, the mainstream drying process for three in one equipment is vacuum drying. The main factors affecting the vacuum drying process are vacuum degree, drying time, stirring blade characteristics, etc.
The vacuum drying process uses a vacuum system to extract inert gas from the tank, reducing the number of gas molecules and isolating air. It is mainly suitable for materials that are prone to oxidation and deterioration, as well as for evaporating materials that require solvent recovery and heat sensitive materials. Under vacuum conditions, it can reduce the chance of material contamination or inhibit the growth of certain bacteria, making it particularly suitable for drying sterile materials.

Performance characteristics of flat filter washing and drying machine
1. System sealing: The three in one filtration, washing, and drying system is a fully sealed system that can prevent toxic substances from polluting the air and reduce the occurrence of poisoning accidents among operators during production operations in a sealed system.
2. Recycling: Materials and solvents are almost completely recovered, avoiding waste caused by material omission and solvent evaporation, which has great economic benefits.
3. Multi functional integrated operation: filtering, washing, and drying are completed in the same device. The container wall is equipped with a heating jacket to enable drying treatment.
4. Continuous operation: Filtering and drying are carried out in a continuous system without the need to process wet filter cake. The dried product can be mechanically transported to weighing, packaging and other sections.
5. Save manpower: A non-technical personnel with simple training can complete the operation. Opening, closing, automatic feeding, and automatic discharging do not require technical personnel to monitor.
6. Thoroughly cleaned: The three in one filtration, washing, and drying system has the functions of automatic spraying and stirring. The filter cake can be thoroughly cleaned, thereby reducing the amount of wastewater discharged and lowering the cost of wastewater treatment.
7. Clean production: The multifunctional filtration and drying system is equipped with a dust collector to collect the dust generated after drying, which can meet the requirements of clean production.
Technical Parameters Table of Flat Plate Filter Washing and Drying Machine
On site installation photos of flat filter washing and drying machine