Side mixer- Introduction
We can calculate the power accuracy of this type of agitator at different Reynolds numbers through 3D simulation and obtain the power curve; By analyzing the velocity field at different positions inside the groove, accurate selection and design can be made.
Side mixer- Overview
Side feeding agitators are widely used in industries such as flue gas desulfurization, petrochemicals, and papermaking, especially when a small amount of power is input into large storage tanks, which can achieve good stirring effects. In recent years, computational fluid dynamics (CFD) methods have been widely used to study the flow characteristics inside stirred tanks. Numerical simulation can not only obtain local information that cannot be obtained by experimental methods, but also save research costs, making it a hot topic in agitator research. Domestic and foreign scholars' research in the field of mixing mainly focuses on top inlet mixers, with relatively few reports on side inlet mixers. Asgharet used RNG turbulence model to simulate the flow field and mixing time of two types of crude oil mixing tanks under the action of a single-sided feed agitator, and the calculated results were consistent with the experimental measurement results. Salwan et al。 The pulp mixing tank under a single-sided inlet mixer was analyzed using Fluent software and ultrasonic Doppler velocimetry (UDV) technology.
technical summary
(1) The power accuracy of the side entry agitator varies with the Reynolds number Re in different flow regions, and the trend of variation is different. In the laminar flow zone, there is a linear relationship between NP and Re; In the transition flow zone, NP varies in a curve with Re; In the turbulent region, the NP value remains around 0154. For the transition flow zone, the results calculated by laminar and turbulent methods are not significantly different. Therefore, in the transition flow zone, the laminar method can be used to calculate the stirring power.
(2) The fluid flow velocity in the mixing tank is only higher near the four blade areas in the lower part of the mixing tank, while the fluid flow velocity in the middle and upper parts of the mixing tank is lower; The volume of the area with a flow rate less than 014m/s accounts for about 80% of the total volume of the water tank.
(3) Under the action of two main types of flow agitators, the liquid form in the water tank is as follows: firstly, the bottom of the central fluid flow channel flows upward towards the liquid surface and towards the surrounding cabin walls, and then the upward and downward circulating flow flows through the bottom of the slot wall slot; The other is the circumferential flow around the tank axis at the bottom of the tank.
Side mixer- Equipment parameters
1. Model number
2. Rotational speed
3. Power
4. Axis length
5. Blade form, diameter, and number of layers
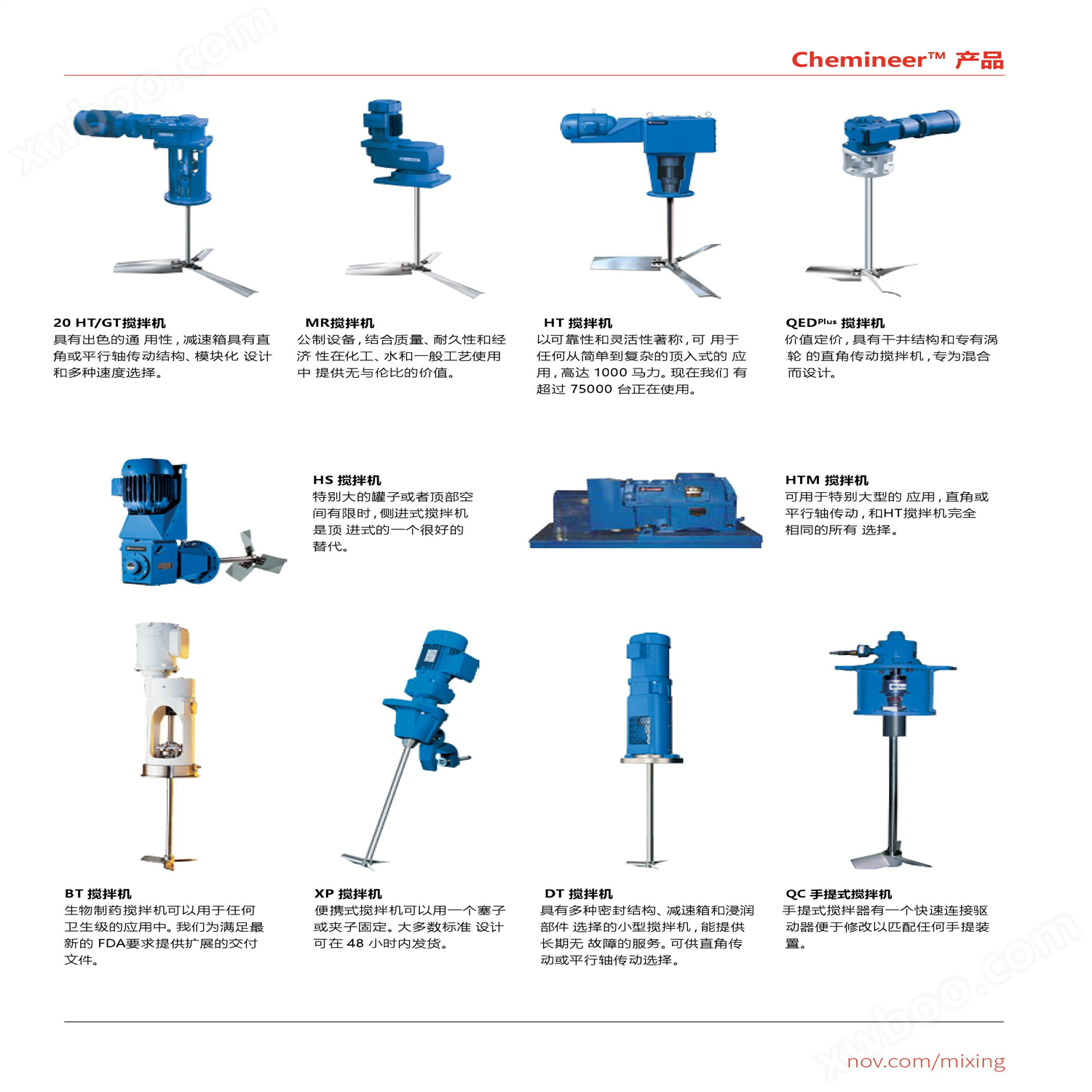



6. Bending moment and torque
7. Interface size
8. Installation location
9. Installation inclination angle
10. Sealing method