
Machine features and standard configuration:
The frame adopts a fully welded steel structure with sufficient strength and rigidity, and is treated with aging to ensure the overall accuracy of the machine tool for long-term use.
Adopting a large floor boring and milling machine, using a one-time processing method for precision machining to ensure machining accuracy.
The bending machine is equipped with an A62 simple CNC system device. Feedback counting through high-performance rotary encoder.
The rear gear adopts ball screw automatic positioning with high accuracy, and the rear gear can be manually adjusted.
Equipped with a front feeding device.
The hydraulic integrated system of the equipment adopts Shanghai Shaker products, and the main oil cylinder sealing ring adopts German SKF/American PARKER original sealing ring, with superior sealing performance, reliable operation, and long service life.
3.2 Use high-quality pipe fittings to ensure that the hydraulic pipeline is leak free.
The hydraulic oil tank made of special oil resistant materials can easily achieve extremely high cleanliness, ensuring the stable operation of the hydraulic system.

name |
numerical value |
Company |
100/3200 |
Nominal pressure |
1000 |
KN |
Workbench length |
3200 |
mm |
Distance between columns |
2500 |
throat depth |
320 |
mm |
Slide stroke |
120 |
mm |
Adjustment amount of slider stroke |
100 |
mm |
Between the workbench and the slider
Maximum opening height
|
380 |
mm |
The height of the workbench above the ground |
800 |
mm |
Hydraulic system maximum
Nominal pressure
|
20 |
Mpa |
Slide travel speed |
Empty load |
85 |
mm |
work |
13 |
return trip |
110 |
Main motor |
model |
Y132M-6 |
power |
11 |
kw |
speed |
960 |
r/min |
Sliding block adjustment motor |
model |
AO2-7114 |
|
power |
0.18 |
kw |
speed |
1400 |
r/min |
Rear blocking material
adjust
Motor
|
model |
Y802-6 |
|
power |
0.55 |
kw |
speed |
910 |
r/min |
Plunger pump |
model |
MCY14-1B |
|
flow |
25 |
L/min |
pressure |
25 |
Mpa |
External dimensions |
long |
3260 |
mm |
wide |
1650 |
mm |
high |
2650 |
mm |
Machine weight |
7550 |
kg |
Equipment working environment:
Power requirements: three-phase four wire system, 380V, 50Hz
Installation site: clean, with less dust
Maximum temperature: 40 º C
Minimum temperature:- 5ºC
Relative temperature: 55-85%
Altitude: below 1000M
This equipment has sufficient strength and rigidity, low noise, smooth operation, and good seismic performance. Under these environmental conditions, it can operate continuously for more than 16 hours.
Machine noise measurement standard:
A-weighted sound pressure level LPA ≤ 82dB (A)
A-weighted sound power level LWA ≤ 94 dB (A)
List of Key Machine Components
Serial number |
Name |
Origin |
1 |
asynchronous motor |
Shanghai Dedong |
2 |
Intermediate relay |
Chint/Siemens |
3 |
Time relay |
Chint/Siemens |
4 |
AC contactor |
Chint/Siemens |
5 |
Low voltage circuit breaker |
Chint/Siemens |
6 |
Oil cylinder seal |
Japan NOK |
7 |
Hydraulic integrated system |
Shanghai Second Hydraulic Parts Co., Ltd |
8 |
Cylinder |
Shanghai Chengjie |
9 |
Scissor machine plunger pump/bending machine gear pump |
Shanghai Shaq |
10 |
Bending machine mold (material: 42CrMo) |
Shanghai Jinshan Machinery Blade Factory |
11 |
Ball screw. linear guide rail |
Taiwan Shangyin |
12 |
Bending machine system (A62 CNC system) |
Hong Kong Sanyuan Automation Co., Ltd |
List of Random Accessories and Supporting Parts
Serial number |
Name |
Code name |
quantity |
1 |
Anchor bolts |
GB799-88 |
4 sets |
2 |
Hexagon nut |
GB41-86 |
4 sets |
3 |
Flat washer |
GB95-86 |
4 sets |
4 |
Spring washer |
GB93-87 |
4 sets |
5 |
Pad board |
|
4 sets |
6 |
Oil gun |
JB288-60 |
1 set |
7 |
Foot switch |
|
1 set |
List of Random Technical Documents
Serial number |
Name |
quantity |
1 |
Machine Tool User Manual (Mechanical Section) |
One copy |
2 |
Machine Tool User Manual (Hydraulic Section) |
One copy |
3 |
Machine Tool User Manual (Electrical Section) |
One copy |
4 |
Electrical schematic diagram of machine tool |
One copy |
5 |
Hydraulic schematic diagram of machine tool |
One copy |
6 |
Machine tool foundation diagram |
One copy |
7 |
Machine tool installation, transportation, and lifting diagram |
One copy |
8 |
Packing List |
One copy |
9 |
Certificate of Machine Tool Qualification |
One copy |
Note: The above documents are bound in the same volume |
Main motor |
Concentric mold |

|

|
Quick fixture |
Rear end department |

|
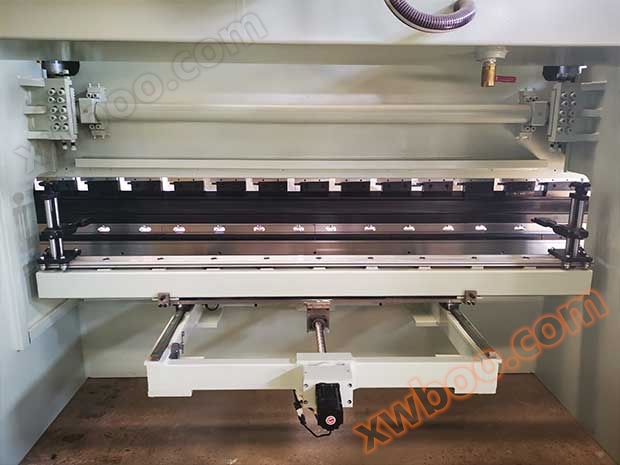
|
operating system |
|
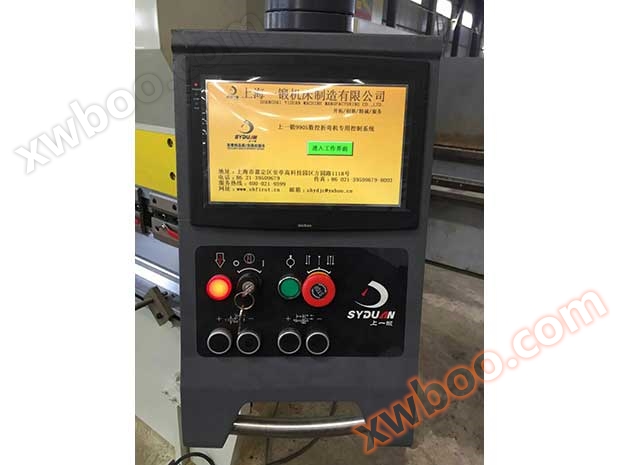
|
|
|
|
|
|
Quality, Service, and Commitment:
1. Product compliance labeling (including but not limited to)
GB17120-1997 "Safety Technical Conditions for Forging Machinery"
GB 5226.1-2002 General Technical Conditions for Mechanical Safety Mechanical Electrical Equipment
GB 16754-1997 "Design Principles for Emergency Stop of Mechanical Safety"
JB/T 1829-2014 General Technical Conditions for Forging Machinery
GB/T3766-2001 "General Technical Conditions for Hydraulic Systems"
JB/T14349-92 "Technical Conditions for Sheet Metal Bending Machines"
GB/T14349-1993 "Precision of sheet metal bending machines"
2. The warranty period for the quoted equipment is 12 months from the date of acceptance, and lifelong service is provided.
3. The quoted equipment must be brand new, unused, and qualified products produced in 2015, with quality and technical indicators meeting the technical requirements specified in the current national standard documents.
During the warranty period, if it is confirmed that there are product quality issues, the quoting party shall bear the liability for breach of contract such as free repair, replacement, and return.
4. Receive the buyer's service notification and arrive on-site within 24 hours to resolve the issue.
5. Special commitment: Upon expiration of the warranty period, a lifetime warranty will be implemented, and no repair fees will be charged. Only the cost of parts will be charged. The service time for reporting repairs is within 24 hours.